Spécialiste de la livraison à domicile de produits alimentaires, Maximo a récemment transféré vers un bâtiment neuf de 17.000 m² son centre de préparation de commandes proche d’Alençon (61) en l’équipant d’un système intralogistique global, conçu et intégré par Transitic. Avec ses racines remontant à la fin du XIXème siècle, cette société familiale basée à Reims s’est développée sur le créneau de la livraison à domicile sous l’enseigne Maximo depuis les années 70, d’abord sur le volet épicerie, puis la décennie suivante sur le surgelé. Elle compte aujourd’hui plus de 500.000 clients desservis dans une soixantaine de départements via son réseau d’une cinquantaine de sites alimentés par deux centres de préparation de commandes, l’historique à Verdun, et le second implanté dans l’Orne il y a une trentaine d’années en se concentrant sur l’offre en surgelé (un millier de références). C’est l’activité de ce dernier qui est transférée sur le nouveau site de Cerisé, afin d’« optimiser les flux logistiques, améliorer les postes et les conditions de travail, notamment en ergonomie, et ainsi gagner en productivité », résume Éric Balon, le directeur logistique du groupe. Et c’est un véritable « concentré d’innovations » qu’a mis en œuvre Transitic en mobilisant l’ensemble de ses savoir-faire « mécaniques, électroniques, informatiques et robotiques », énumère Jérôme Paque, directeur Projets au sein du spécialiste de l’intralogistique. La zone de lancement comporte ainsi deux formeuses multiformats, avec un volet étiquetage et scan pour assurer la traçabilité de chacun des cartons (jusqu’à 1.200 sont préparés par heure). En zone de picking, les armoires réfrigérées où les opérateurs prélèvent les produits sont équipées de quelque 1.150 balises pick-to-light et d’écrans de contrôle, et la ligne qui parcourt les différentes stations est surplombée d’un convoyeur à bande pour évacuer pas moins de 16.000 cartons fournisseurs chaque jour (acheminés vers des compacteurs). Après une étape de contrôle, notamment pondéral, les cartons préparés filent vers une cellule à -25°C hébergeant un buffer-séquenceur composé de 10 lignes de convoyeurs qui les stocke en les triant par tournée (supprimant ainsi les contraintes de séquençage en amont). Et c’est enfin dans une zone à 5°C que 5 robots palettiseurs chargent lesdits carton sur des rolls dans leur ordre de livraison, avant de partir en zone d’expédition. Le tout est piloté par les solutions Open WCS et Open SCP de Transitic. MR
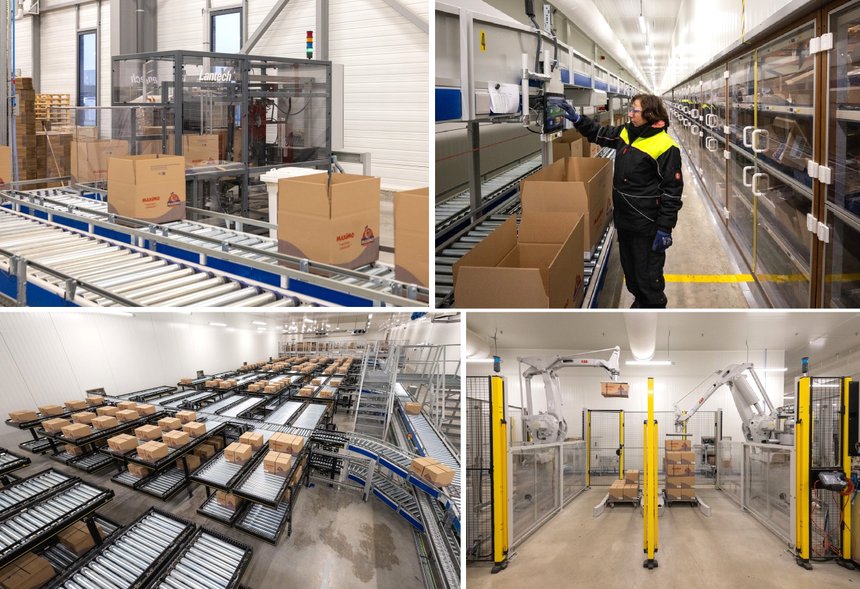
L’installation conçue et mise en œuvre par Transitic sur le site dédié aux surgelés de Maximo à Cerisé (61) couvre l’intégralité du cycle de préparation de commandes. © Transitic / ACHphoto